Francuskie instytut energii słonecznej INES opracował nowe moduły fotowoltaiczne z termoplastiami i naturalnymi włókienami pochodzącymi w Europie, takimi jak llek i bazalt. Naukowcy mają na celu zmniejszenie śladu środowiskowego i masy paneli słonecznych, przy jednoczesnym poprawie recyklingu.
Z przodu z przodu panelu z recyklingu i kompozyt lniany z tyłu
Zdjęcie: GD
Z magazynu PV France
Naukowcy z Francji National Solar Energy Institute (IES)-oddział francuskiej alternatywnej energii i Atomic Energy Commission (CEA)-opracowują moduły słoneczne zawierające nowe materiały biologiczne z przodu i tylnych stron.
„Ponieważ ślad węglowy i analiza cyklu życia stały się teraz istotnymi kryteriami w wyborze paneli fotowoltaicznych, pozyskiwanie materiałów stanie się kluczowym elementem w Europie w ciągu najbliższych kilku lat”, powiedział Anis Fouini, dyrektor CEA-ines , w wywiadzie dla magazynu PV France.
Aude Derrier, koordynator projektu badawczego, powiedziała, że jej koledzy przyjrzeli się różnych materiałów, które już istnieją, aby znaleźć takie, które mogłyby pozwolić producentom modułów na produkcję paneli, które poprawiają wydajność, trwałość i koszty, jednocześnie obniżając wpływ na środowisko. Pierwszy demonstrator składa się z heterOjction (HTJ) ogniw słonecznych zintegrowanych z materiałem kompozytowym.
„Przednia strona jest wykonana z polimeru wypełnionego włóknem szklanym, który zapewnia przejrzystość”, powiedział Derrier. „Tylna strona jest wykonana z kompozytu w oparciu o termoplastiki, w których zintegrowano tkanie dwóch włókien, lnu i bazaltu, co zapewni siłę mechaniczną, ale także lepszą odporność na wilgotność”.
Lek pochodzi z północnej Francji, gdzie cały ekosystem przemysłowy jest już obecny. Bazalt pochodzi z Europy i jest tlejący przez partnera przemysłowego Ines. Zmniejszyło to ślad węglowy o 75 gramów CO2 na wat, w porównaniu z modułem odniesienia o tej samej mocy. Waga została również zoptymalizowana i wynosi mniej niż 5 kilogramów na metr kwadratowy.
„Ten moduł jest skierowany do PV na dachu i integracji budynków” - powiedział Derrier. „Zaletą jest to, że ma naturalnie czarny kolor, bez potrzeby tylnego arkusza. Jeśli chodzi o recykling, dzięki termoplastikom, które można pamiętać, rozdział warstw jest również technicznie prostszy. ”
Moduł można wykonać bez dostosowania bieżących procesów. Derrier powiedział, że chodzi o przekazanie technologii producentom bez dodatkowych inwestycji.
„Jedynym imperatywem jest posiadanie zamrażarki do przechowywania materiału i nie rozpoczęcie procesu sieciowania żywicy, ale większość producentów używa dziś prepreg i jest już do tego wyposażona”-powiedziała.
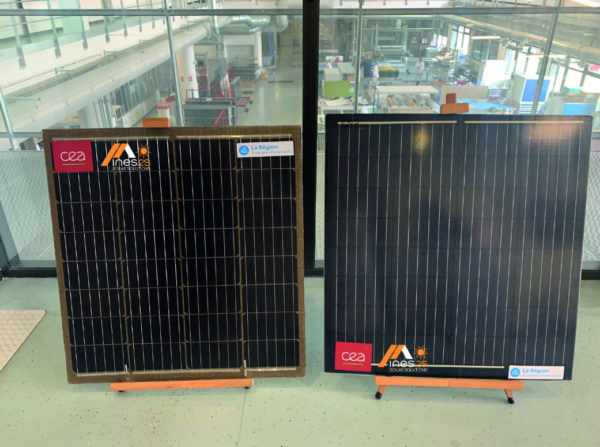
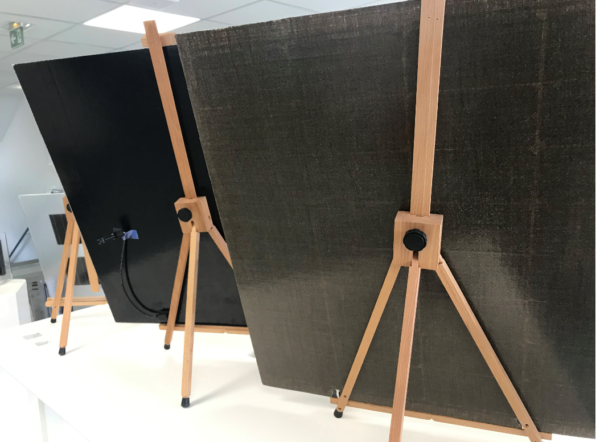
„Pracowaliśmy nad drugim okresem życia szkła i opracowaliśmy moduł złożony z ponownego wykorzystanego szkła 2,8 mm, który pochodzi ze starego modułu”, powiedział Derrier. „Zastosowaliśmy również enkapsulację termoplastyczną, który nie wymaga sieciowania, który będzie łatwy do recyklingu, i termoplastyczny kompozyt z włóknem lnianym do oporu”.
Bazaltowa tylna twarz modułu ma naturalny kolor lniany, który może być estetycznie interesujący dla architektów pod względem integracji fasad. Ponadto narzędzie do obliczania Ines wykazało 10% zmniejszenie śladu węglowego.
„Obecnie konieczne jest zakwestionowanie fotowoltaicznych łańcuchów dostaw” - powiedział Jouini. „Z pomocą regionu Rhône-Alpes w ramach Międzynarodowego Planu Rozwoju, poszliśmy zatem szukać graczy spoza sektora słonecznego, aby znaleźć nowe termoplastiki i nowe włókna. Myśleliśmy również o obecnym procesie laminowania, który jest bardzo energooszczędny. ”
Pomiędzy ciśnieniem, fazą prasową a fazą chłodzenia laminowanie trwa zwykle od 30 do 35 minut, z temperaturą roboczą od około 150 ° C do 160 C.
„Ale w przypadku modułów, które coraz częściej zawierają ekologiczne materiały, konieczne jest przekształcenie termoplastii w odległości około 200 ° C do 250 ° C, wiedząc, że technologia HTJ jest wrażliwa na ciepło i nie może przekraczać 200 ° C”, powiedział Derrier.
Instytut badawczy współpracuje ze specjalistą od termokompresji indukcyjnej z opartą na Francji Roctool, aby skrócić czasy cyklu i tworzyć kształty zgodnie z potrzebami klientów. Razem opracowali moduł o tylnej twarzy wykonanej z termoplastycznego kompozytów typu polipropylenu, do którego zintegrowano włókna węglowe z recyklingu. Przednia strona jest wykonana z termoplastii i włókna szklanego.
„Proces termokompresji indukcyjnej Roctool umożliwia szybkie podgrzanie dwóch przednich i tylnych płyt, bez konieczności osiągania 200 ° C u podstaw komórek HTJ”, powiedział Derrier.
Firma twierdzi, że inwestycja jest niższa, a proces może osiągnąć czas cyklu zaledwie kilka minut, przy użyciu mniejszej energii. Technologia jest skierowana do producentów kompozytowych, aby zapewnić im możliwość produkcji części różnych kształtów i rozmiarów, jednocześnie integrując lżejsze i bardziej trwałe materiały.
Czas po: 14 czerwca-201022